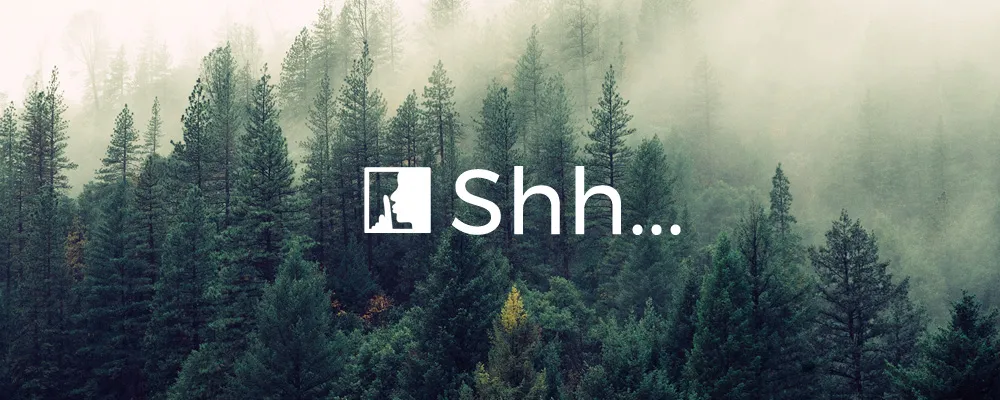
The “Secret” Bao Living Master Plan: Part One.
A little back story for this blog post. It contains the main motivation and strategy behind our company Bao Living. The first draft was written in May 2016. Back then we hadn’t communicated anything about Bao Living or the idea behind it so we decided to not yet publish it. Today (June 2017) this, with the publication of our new website, has changed. Furthermore quite recently a large industrial party has validated Bao Living, and endorsed our macro analysis and vision. So we thought the time to publish this post had arrived. All feedback is welcome, and more importantly, enjoy the read!
The motivation behind Bao Living is to “rethink construction”. To specify this goal: we are going to help expedite the move from today’s rather costly, polluting and stressful construction method towards more affordable and environmentally conscious housing solutions.
Why do we focus so strongly on helping to realize this move? Is this actually going to do some good for the world? We think it will and our reasoning for this is explained below:
- Affordability
The cost of buying or constructing a home has been steadily increasing during the past 3 decades. In Belgium, for example, this has resulted into a 78% average cost increase between 2000 and 2013 (excluding land). If this trend continues more and more families will not get the chance to purchase and own a home. This is bad because home ownership is a big contributor to long term economic prosperity. - Sustainability
We currently see two main challenges in the area of construction sustainability:
i. The building sector contributes up to 30% of global annual greenhouse gas emissions and consumes up to 40% of all energy. In order to realize a truly sustainable economy we, as a society, need to realize that we must tackle these two problems. These two figures are the main reason why Europe has decided that in 2020 every new built construction needs to be passive in nature.
ii. Observational research has shown that the amount of construction waste can be as high as 10 to 15% of the materials that go into a building. There exists a considerable variability between construction sites, however there is huge opportunity and urgency to reduce this waste. By doing so we remove the needless and avoidable environmental impact that also negatively influences the cost of construction.
How is Bao Living going to contribute in tackling these two challenges? After 18 months of R&D we developed a first product, named SAM, that has a significant positive impact on the two problems explained above. Our research has shown that a large part of the current costs are incurred because of the inefficient way houses are designed and utilities are installed. With SAM we believe we can do it more efficiently.
Through holistic reasoning we came to the conclusion that one can distinguish two categories of components in a building: structural components (walls, stairs, roofs, windows, doors …) and technical elements (heating, ventilation, sanitation, electricity, ….). We believe efficiency can be dramatically increased by separating these two as much as possible. In fact, with our first product, we aim to do so completely.
SAM will be a factory produced module that contains all the utilities (telecom, heating, ventilation, electricity and sanitation) as well as a kitchen and bathroom. The implementation of this product can realize dramatic savings in comparison with traditional, manual labor intensive, construction techniques. It does however need to be stressed that SAM is more than just an integrated kitchen or bathroom. It integrates ALL utilities in such a way that the structure of a building solely has a load bearing and insulating function.
To tackle the Affordability issue highlighted above, Bao Living will:
- Manufacture SAM in an automated production environment.
Automation leads to a significant lowering in costs, especially once we benefit from economies of scale. This product is definitely aimed at mass production. - Drastically reduce construction times.
Currently the average construction duration in Belgium is 18 months. A minimum 6 of these 18 months are necessary for the installation of the building utilities. SAM however can be installed in 3 days per apartment. This represents a dramatic lowering in construction time. For example: the utilities of a 20-apartment construction project can be installed, by a 2-person team, in 60 (business) days/3months. If another installation team would be aded the installation time would be halved again. - Dramatically lower the margin of error.
Currently, the 5 main utilities are installed by as many suppliers. This combined with the lack of digital plans and integrated communication tools leads to a very high margin of error. Studies indicate that the costs of these errors can run up to 10% of the total construction project price. Because we provide all the utilities in one, factory assembled, system this error margin will drastically lower. Again saving significantly on costs.
SAM will also produce drastic improvements for the two main Sustainability challenges:
- It will remove the necessity of manually installing the different utilities on site. If our module is combined with prefabricated walls it will almost completely remove the 15% material waste that is currently considered standard in the sector. Less material wasted = lower ecological impact.
- Our concept has been designed to be compliant with the 2021 norms: (Nearly Zero Energy Buildings legislation). By doing so we will be one of the more progressive solutions on the market. This means, for one, the basic version will include non fossil fuel based heating solutions and a heat recovery ventilation system.
- A third aspect of sustainability, that we can’t forget with SAM, is the fact that the majority of the “active” elements are decoupled from the “passive” elements. This means that end-of-life disassembly or deconstruction is much less painful. The utilities are no longer built or ingrained into the structure of the building. This makes refurbishment or renovation much easier. This is highly important because lengthening the useful life of a structure is the most environmentally responsible way of getting the most out of the energy embedded in the construction materials.
We are fully aware of the fact that Bao Living isn’t a “lean” startup. It’s success is based on an innovative design manufactured in a mass production environment. We need to have access to such an environment from the start. Therefore we needed to identify construction partners who already own the necessary equipment. This is what we did in the first quarter of 2016. Three partners are currently linked to the production of SAM : a design studio, a high volume kitchen and bathroom manufacturer and a wholesaler of heating and ventilation installations.
Another strategic decision we made is to focus on the B2B market. By doing so we can better focus on the further development and improvement of SAM and we avoid the investment of a B2C marketing approach.
However, as mentioned above, one of the main goals of Bao Living is to lower the cost of living. With this in mind it could become mandatory to develop our own B2C projects to insure that the realized cost savings will reach the end consumer instead of solely increasing the real estate developer’s profit margin.
So, in short, our master plan is:
- To build a SAM prototype.
- To validate our theoretical assumption on this prototype.
- To sell SAM’s to a B2B market (Project developers, building companies,… )
- To continuously invest in R&D to increase the functionality and the efficiency of SAM.
- In the long run, invest earnings into other products that can help expedite the move from rather costly, polluting and stressful construction techniques towards more affordable and ecological housing solutions.
Don’t tell anyone…
Team Bao
P.S. If you, or your company, recognizes itself in the above mentioned goals feel free to contact us. We are looking forward to building a community of equals that are potentially complementary.
P.P.S Because this blog was written in May 2016 we have made some progress on the above mentioned 5 step plan. Point 1 and 2 have been realized and we are currently working intensely on point 3.
P.P.P.S A little update at the beginning of 2019 (the 18th of January to be precise). We recently finished our first commercial SAM unit. (To watch a little clip about it click here). And we have 3 more SAM’s that are going to be installed in the next 60-ish days. So we are now fully in the third part of the above described plan. We are already halfway into part four to be precise. Almost time to start looking a bit more in detail into part 5. More about this in the near future…